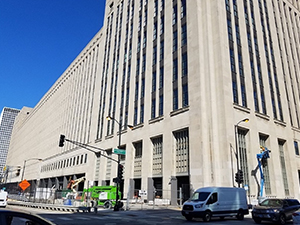
Many words and phrases could be used to describe Chicago’s Old Post Office: bygone communications hub, historical gem, 1920s architectural marvel, and, until a few years ago, drafty. Despite its designation as a Chicago City Landmark, the Old Post Office spent the years between 1996 and 2016 vacant and exposed to the city’s harsh elements.
When the building was finally acquired by a developer for remediation, it had spent the past two decades welcoming rain, snow and sleet through its cracked windows and leaky roofs. The extreme damp that had seeped into the building’s bones needed to be reversed before the building’s first major tenant – Walgreens – was scheduled to move in.
With an $800 million budget and tight timeline, the remediation – the largest historic adaptive reuse project in the country to date – needed to go off without a hitch. Unfortunately, retrofitting the 2.3 million square foot building with a 21st century hydronics system was a feat of engineering.
Creative Hydronics Solution Keeps Project on Track
Figuring out a way to maintain a comfortable temperature throughout the hulking, historical building was a feat. Maddock Industries, McGuire Engineers and F.E. Moran were brought in to design a hydronics system that would keep indoor temperatures stable, regardless of fluctuations in Chicago’s fickle – and often extreme – weather.
The building’s layout – composed of three connected buildings – made the hydronics design and installation all the more difficult. Each building (north, south and east) posed its own, unique challenges when it came to climatization. Those challenges were most acute in the north building – the tallest and narrowest of the three.
Per the hydronics plan, each floor of the north building was to have its own loop of chilled water and two tertiary Armstrong pumps. The compact nature of each floor meant that engineers had little space to work with: each pump room was about the size of “an old coat closet,” according to Michael Moxon, VP of Maddock Industries. Because of that, there wasn’t room to install check valves to prevent water from backflowing.
As Maddock sales engineers anticipated, water did start flowing backwards once the pumps were installed – which short-circuited the system. Luckily, the hydronics experts at Maddock Industries had a solution up their sleeve that stopped the system from short circuiting and delivered perfect temperature control throughout the building.
Learn How It Was Done
Read the case study to learn about the inventive solution Maddock devised to stop the north building’s pumps from short-circuiting. To learn more about the Armstrong pumps Maddock Industries has in stock, contact us.