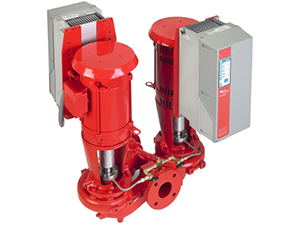
Rising energy costs and sustainability governance are driving the development of new technologies to improve the performance of buildings. Armstrong has answered the challenge with unparalleled pumping efficiency and performance by combining Design Envelope (DE) vertical inline (VIL) pumps, motors and intelligent variable speed (IVS) controllers.
How IVS Works
In a chilled water system, a building’s temperature controls influence the local flow of control valves modulating flow to the cooling coils (load). As the control valves open for more chilled water flow, the differential pressure across the valve decreases. Armstrong controllers react instantaneously to this change by increasing the pump speed. If the control valves close to reduce the chilled water flow, the differential pressure across the valve increases and the controller reduces the pump speed and draws only the power required to meet that demand.
As a result, the “intelligent” action of Armstrong IVS saves energy every minute the pump is on: the drive and the motor are mated/configured to work better together, resulting in ideal pump efficiency vs. the need for increased speed, horsepower and energy. Armstrong Design Envelope pumps feature the largest impellers available, which are more efficient, so you don’t need to run a trimmed impeller at full speed. This requires less energy and gives you more flexibility in the capability of the pump.
Sensorless IVS Control
Equipped with the sensorless design feature, Armstrong DE IVS pumps don’t require an external sensor to monitor and control the HVAC load.
Monitor Power & Speed, Control Head & Flow
Equipped with the sensorless IVS, the Armstrong DE pump performance characteristic curve (power draw and RPM) and operating curve are pre-programmed into the controller. During operation, the controller monitors the power and speed of the pump and establishes the hydraulic performance and position of the pump’s head-flow condition relative to the system requirements. As the building’s control valves open or close to regulate flow to the cooling coils and maintain building occupant comfort, the sensorless IVS controller automatically adjusts the pump speed to match the required system pressure requirement at the current flow.
A Multitude of Benefits
Design Engineers
- Broad range of performance leads to reduced iterations of pump selection
- Energy-saving solution reduces HVAC operating costs
- Contributes to LEED certification
- Improved pumping efficiency and control leads to reduced carbon footprint
- Simpler HVAC system drawings with fewer components and reduced wiring
- Sensorless IVS technology means fewer components to select
Contractors
- Less floor space required
- Fewer peripheral components to install
- Reduced costs for pipe and pipe installation
- No requirement for a concrete pad
- Faster installation and commissioning
Building Owners
- Reduced energy consumption leads to substantial operating savings
- Lowest pump lifecycle costs
- Green building incentives and rebates available in most regions
- Demand-based variable speed leads to improved occupant comfort
- Selection methodology provides future proofing against changing building loads
- Selection methodology prevents oversizing of equipment
Get a Quote Today
As a result, IVS offers material and labor savings during project installation as well as energy, cost and carbon savings during operation over standard pumping practices such as constant speed or variable-frequency drives. Sensorless control eliminates the need for sensors, wiring and time-consuming commissioning and software intelligence emulates typical sensor-based pumping system control with a differential pressure sensor at the most remote load.
IVS is proven technology that has been used in Armstrong products since 1999 and supports ASHRAE 90.1 energy saving targets.
Contact a Maddock Armstrong product expert to learn more about IVS and Design Envelope pumps to see if they’re the right fit for your next project.